Remote Configuration
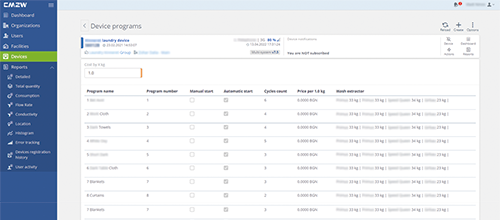
The intuitive interface allows fully remote program configuration which lowers the configuring time spent by 50%, so employees could move their focus from day-to-day basic operations to adding value activities.
Program Setup
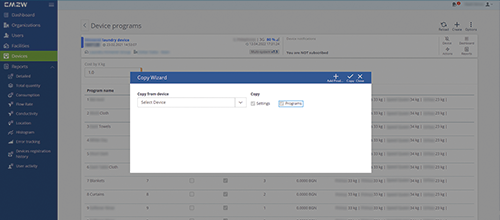
Every washing process allows individual program setup that is quick and intuitive to create. All washing programs could be duplicated from a system library or another device in the organization.
Schematic Settings
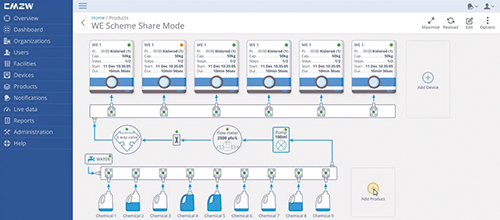
Each user has the ability to visually configure programming settings and modify programs. All system components are displayed for easier perception and use of information, so individual programming options could be laid out more quickly and accurately.
Template Based Setup

The reusable self-designed application settings allow the user to customize the platform interface and improve time management efficiency. All operational and calibration settings could be duplicated from a system library or another device in the organization.
24/7 Connectivity
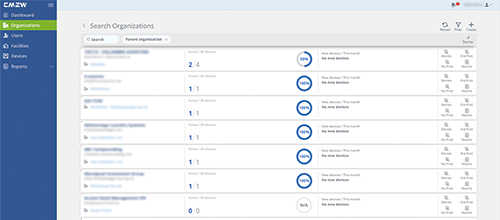
All changes initiated by users using schematic programing settings apply immediately thanks to the wireless communication with the back-end servers.
Real-Time Tech Support
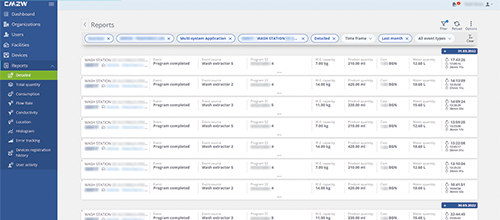
Live support is available 24/7 to ensure everything goes smoothly and no delays or interruptions regarding productivity are observed.
Easy-to-Use Application Interface
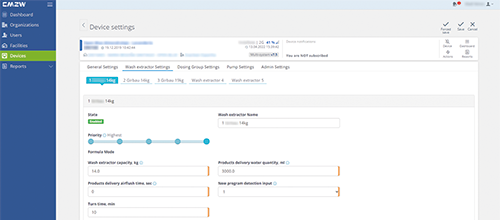
Using the intuitive application program even very complex programming settings could be easily configured without any specific technical qualifications.
Histograms
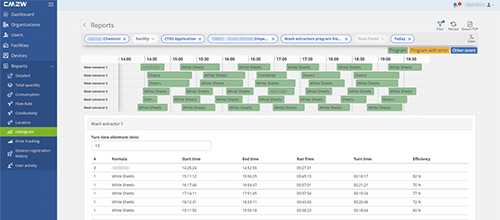
The operationally focused facility histograms keep the dosing process running properly. They deliver real-time dynamic data that is used to guide facility operations and avoid process failure.
Scheduled Dosing
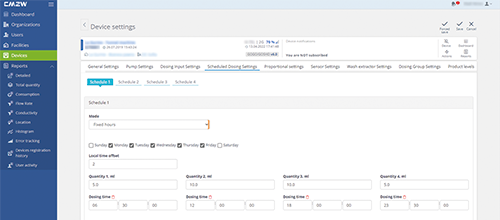
The scheduled dosing mode enables the opportunity to configure two different operating modes to a single system. The fixed-interval dosing mode doses chemicals at regular time intervals and the fixed-time dosing mode – at predefined date and time.
Consumption Monitoring
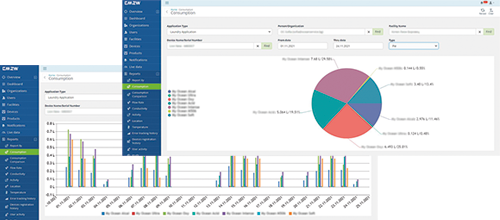
Based on all consumption data generated on chemical, system and facility level you can benefit from a multi-level consumption monitoring to improve consumption estimation and facility effectiveness.
Error Tracking
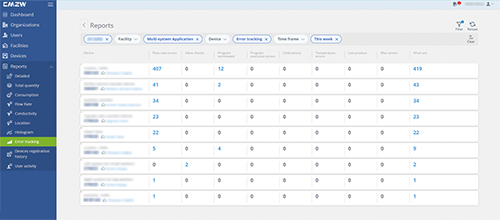
Error tracking provides an overview of the actual errors over the dosing systems on different locations. All system errors are listed hierarchically starting with the most critical ones, so technicians can easily prioritize them and schedule the maintenance effectively according to the error importance.
Flow Rate Monitoring
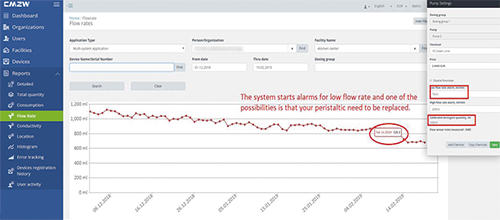
Thanks to the flow rate monitoring you can keep an eye on the performance of all systems to increase customer satisfaction and avoid disruption of the washing process.
Detailed Reporting

The detailed reporting feature provides full performance visibility filtered by organizational structure and enables total revenue estimation by facility, program, etc. and projected to actual revenue assessment.
Scheduled Reporting
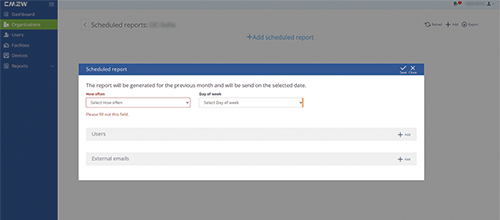
Using scheduled reporting you benefit from up-to-date information on device, facility and organizational level and receive the latest reports about chemical consumption, device error history, stock inventory etc. and make data-driven decisions.
Customized Dashboards
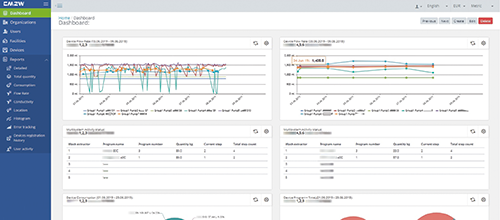
All dashboards are easily configurable and display information from different platform reports like activity status, device flow rate, device consumption, device error tracking, device programs total and device work time widget of all dosing systems.
Progressive Notification Filter (PNF)
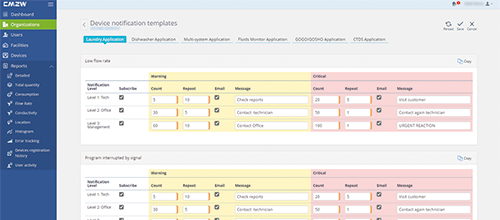
PNF is a unique system for filtering and addressing important notifications like warning alerts to the assigned organizational level ensuring faster reaction time and process optimization. Supported with the right software tools it predicts potential failures and focuses on their prevention.
DATA Transfer
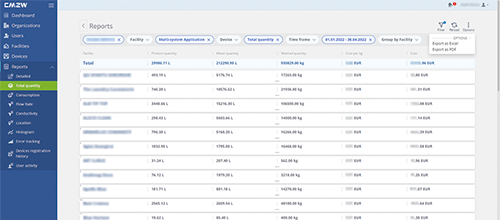
All reports and data storage generated during the washing process could be transmitted to external front-end applications on request.